
NYPH are currently working with the Urban Green Council to provide documentation to the NYC Department of Buildings to get permission for AAVs to be used in NYC construction. Over many years, Air Admittance Valves have been a proven method to improve upon the use of typical vent stack systems both in energy efficiency and construction cost. The reduction in energy use from a high performance thermal envelope will provide cost savings throughout the life of the building: a win for both the owners and the city as a whole. The construction cost savings of eliminating vent stacks, penetration waterproofing, and airsealing stacks can be reinvested into improving the building envelope. Furthermore, fewer vents result in less potential for leaks or failure.Īlthough not in New York City, AAVs have been used for decades and allowed in practically all US jurisdictions as a suitable alternative to plumbing stacks. A typical plumbing vent system requires numerous roof penetrations, which compromise the building’s thermal! envelope (and each require additional insulation/air-sealing work). Additionally, one less vent per stack results in a smaller shaft and more usable square footage (and less air-sealing work). On a larger building-wide scale, fewer vents result in fewer exterior roof penetrations. It eliminates the need for a second vent pipe, reducing construction costs while increasing usable space. The AAV is a non-mechanical valve that is located just above the fixture’s drain, fitting within a bathroom vanity or cabinet, out of view. Air Admittance Valves (AAVs) are one of such products we feel outperforms the typical vent stack system.Īir admittance valves are pressure-activated, one-way valves that can be used in place of typical vent stack systems. However, in this age of increased awareness of energy efficiency and building performance, there are now products and technologies that give us better functional performance, simplify construction and increase energy efficiency. The function and construction of a typical vent stack system has remained the standard in NYC for about a century. It allows air in above the trap, equalizing the pressure on both sides of the trap, thereby allowing it to hold water and keep sewer gasses out of the building. Traditionally, venting is achieved via a second pipe connected to the sewer stack – the vent pipe.
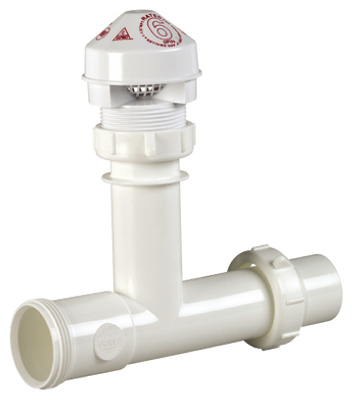
Without a vent pipe, a vacuum effect would result which would draw all the water down from the trap, allowing the noxious gasses to pass through. When a toilet is flushed or sinks and tubs drain water, this water travels down the sewer pipe. Without the trap’s water seal, noxious gasses would make their way up through your pipes, out of the fixtures, and into your home. Vented plumbing stacks are required to maintain a water seal in a fixture’s trap, the U-shaped section of pipe below a sink, which creates an air lock that prevents the entrance of sewer gasses. Venting of plumbing fixtures has been a standard in the design and construction of plumbing systems in New York City buildings for almost a century.
